Sustainability can be defined in many ways. As applied to our goals with Solarhurst, it means to plan, build and operate a very durable well-constructed home, that makes modest demands on energy and material resources, is ergonomically designed and comfortable for all ages and capacities, and coupled with the lifestyle of its occupants, has minimal impact on the local AND global environment. Unfortunately, in the absence of hard objectives, such lofty sentiments mean very little!
Prior to construction, and in consultation with Jorg Ostrowski ( our architect), we established some specific targets, with respect to sustainable building and ongoing operation. Of course at this point in time it remains to be seen whether indeed these targets can be met. It should be noted that of the 67.7 GJ (gigajoules) in anticipated annual energy use, only 9.2 GJ (the propane) is non-renewable and is a net contributor to greenhouse gases (GHG’s). The rest of the energy is to be produced on-site (photovoltaics, solar hot water and managed wood lot). Our electrical will be hybrid solar (grid-tied with battery back-up), and we hope to be a net provider of electricity to the grid (hopefully by at least 9.2 GJ per year to offset the propane).
The projected savings on heat energy seem quite modest and may be significantly underestimated. The wood fuel consumption is predicated on a moderately, not super-insulated building envelope. Hopefully our fuel consumption will be less than the 6000 kg per year indicated. In the winter of 2010-2011, approximately two face cords of fuel were used to keep the house warm. The wood was mostly white ash but had admixtures of other species. This translates to only about 900 kg, however we had a huge snowload on roofs this (year acting as insulation) and the home was only heated to temperatures comfortable for construction. If real consumption was approximately 2000 kg then this translates to only 17.5 GJ and our total energy would sum up to 32 GJ, or 1/3 the Quebec average.
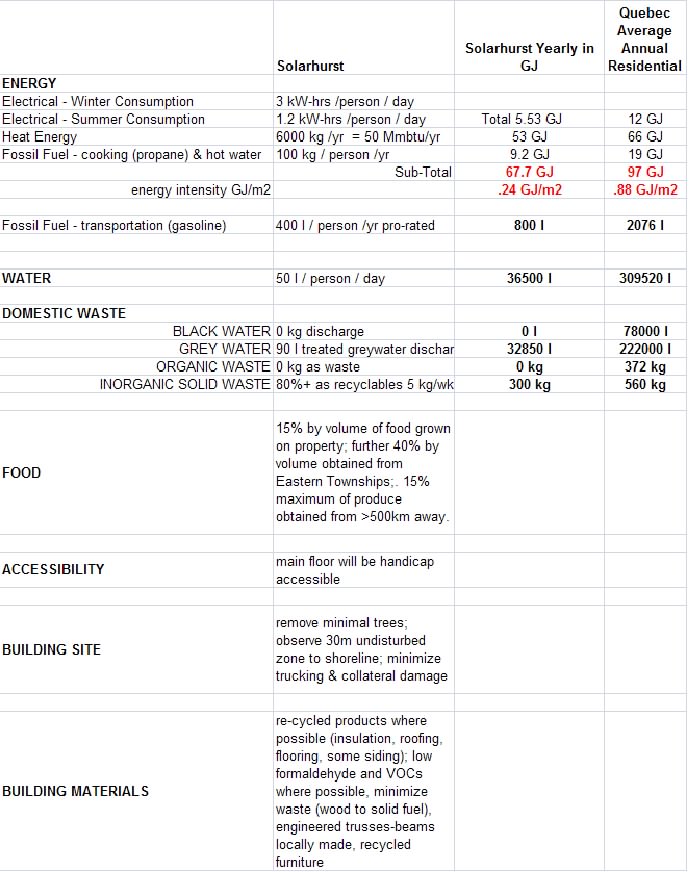
Table 1: Targets for Low Impact Lifestyle
It was also our intent to minimize disruption of the land during construction, minimize any construction traffic, and minimize construction waste. We also wished to use environmentally justifiable building products where possible.
A minimal number of trees were removed. A 30m undisturbed zone (measured from the shoreline – double the required 15m) was respected with the exception of the installation of a 15 x 40 foot leach field, mandated by provincial code.
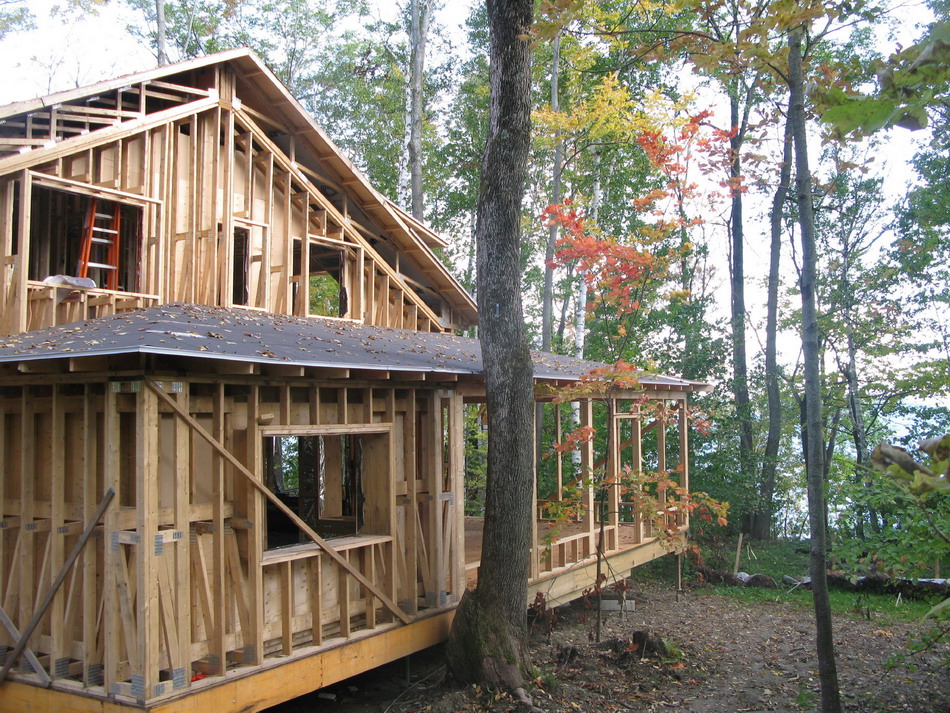
Preservation of mature white ash directly adjacent to west side of house

15 x 40 ft Enviroseptic leach field that encroaches on self-imposed 30m shoreline zone
The number of truckloads, in and out, were not substantially reduced from typical construction, and regrettably the incredibly wet weather in July of 2008 did lead to some minor local road damage. This aspect could have been partially mitigated by using a slab on grade foundation, but for other reasons this option was rejected early on in the design process.
The bulk of the envelope consists of manufactured vertical wall, and horizontal floor/ceiling and roof trusses supported by multi-laminate engineered wood beams. This resulted in minimal on-site wastage of what is, a renewable resource. Full cycle embodied energy and spoilage calculations for these materials was not attempted – although the results of such an exercise would be most interesting! Standard plywood, strand and fibreboard (tentest) were also employed in the roof, walls and subfloors. These products along with the laminated beams contains both VOC’s and formaldehyde, and will have some effect on indoor air quality as they off-gas. For reasons of cost and ease of purchase, alternative products were not pursued. All interior finishing products were zero to low-VOC.
Three important building materials were employed that are wholly, or at least largely, composed of recycled materials. These are the Enviroshake roofing tiles (recycled used tires), Amerrock mineral wool insulation (recycled slag), and elm hardwood flooring (recycled old barn beams). The first two are discussed in more detail elsewhere on the webpage.
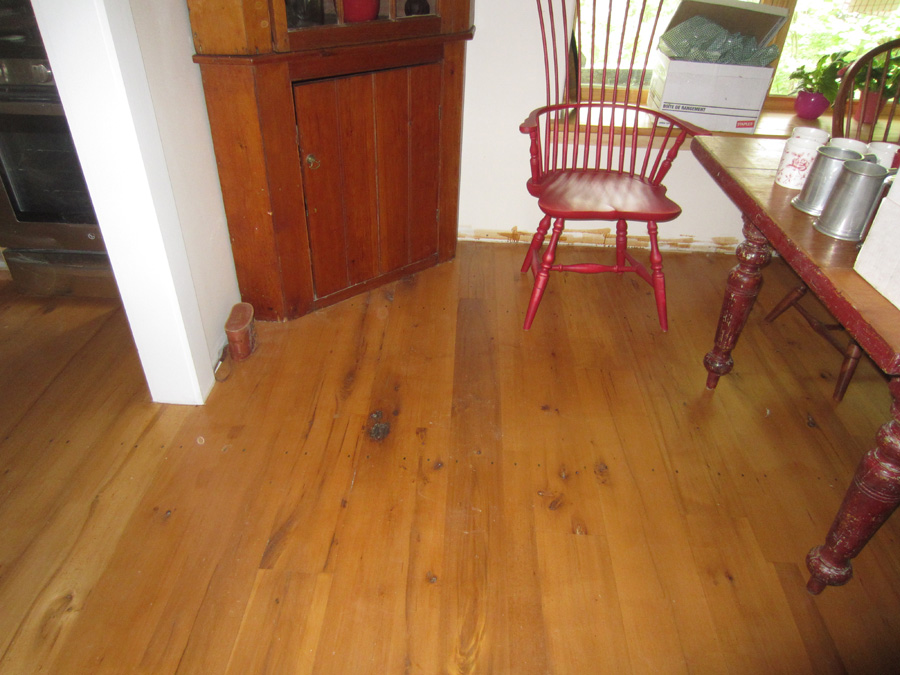